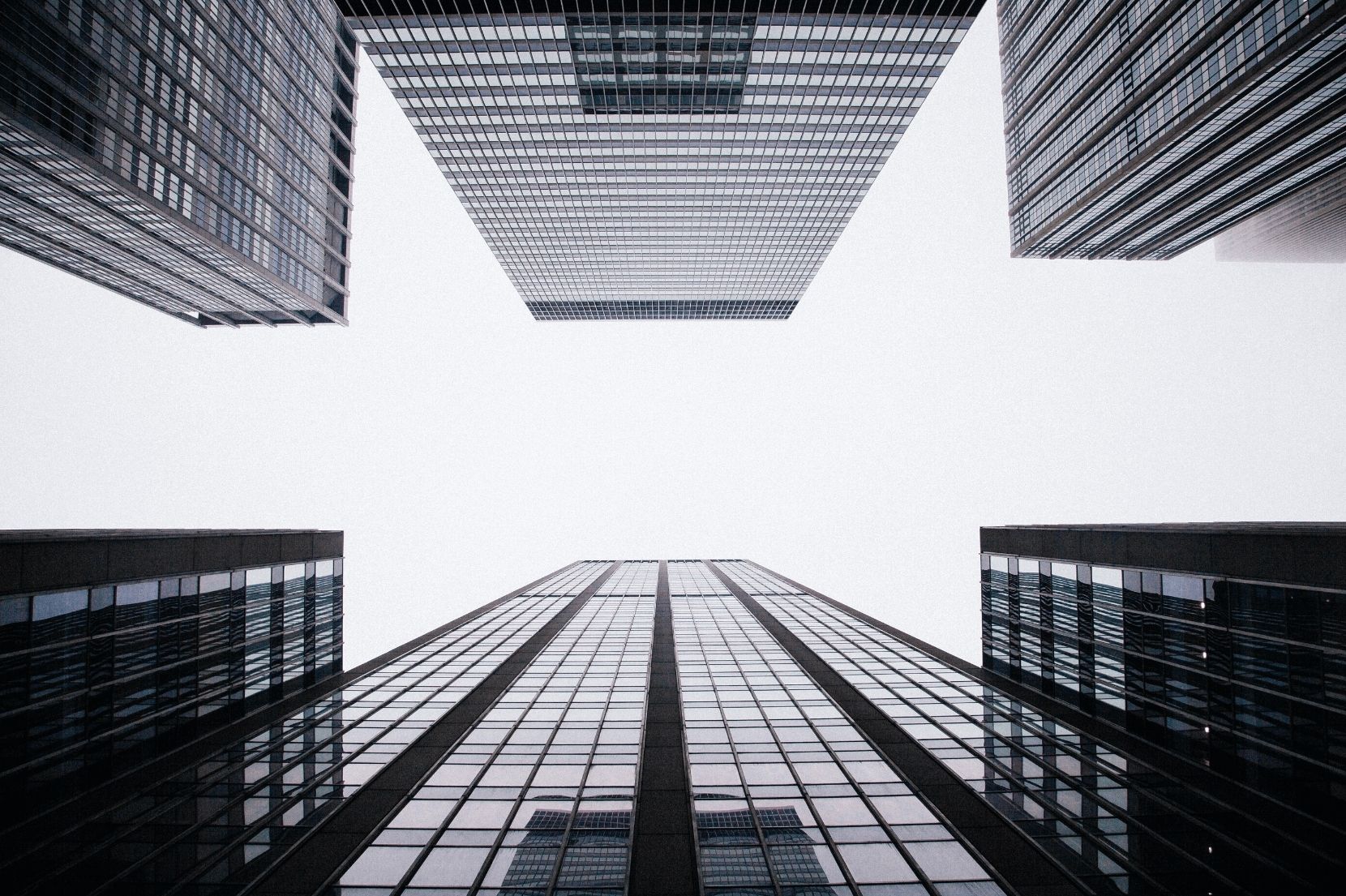
Digital twins and Industry 4.0
Digital Twins are digital replicas of objects, places, physical systems or processes. Everything can be artificially represented. And the digital twin is responsible for truthfully showing the operation, response and behavior of its “real” counterpart through the combination of physical and virtual data.
One of its original examples can be found in NASA and the large-scale representations of its space capsules used to simulate all kinds of scenarios from a secure environment.
This technology has not stopped evolving since then, and today taking advantage of this type of resource is much easier thanks to the arrival of the IoT, which is generating a scenario full of possibilities for all types of industries.
The incorporation of sensors in products and assets has opened up access to huge amounts of data, generating the basis for digital twins. And technologies such as Big Data, the Cloud and Augmented or Virtual Reality, have enhanced its functionality.
Today, it is already possible to access a digital display of the detailed status of an entire plant and those elements integrating it. And digital twins can be equipped with Machine Learning so that they can learn and react autonomously. It’s no longer a matter of collecting data. It’s about managing it and learning from it.
It is in the scenario generated by the Digital Twins, made up of the conjunction of the physical world and the digital world, where it is possible to analyze all kinds of data. The Digital Twins integrate artificial intelligence, machine learning, advanced analytics, and spatial networks, and incorporate all kinds of data obtained through the use of sensors, promoting preventive/predictive maintenance and offering the possibility to check the response of our assets in all sorts of scenarios (avoiding destructive testing).
The world is living a change of era with the so-called Industry 4.0. A concept driven by the use of the latest technologies and focused on generating a business culture based on continuous improvement and innovation. An unthinkable goal until the appearance of the IoT.
Connectivity of devices and sensors, homogenization, reprogramming, deployment and management of sensors and of volumes of information are the great challenges in this type of project. But these are no longer insurmountable challenges. Inevitably, as the Internet of Things becomes part of our environment, digital twins become the cornerstone of any industrial automation process.
An example of this is our collaboration with Acciona, a world leader in renewable energies, which promoted the creation of a Digital Twin of one of the largest solar plants in the world with the aim of improving its efficiency and management. The development of a Supervisory Control and Data Acquisition (SCADA) system allowed us to obtain real time control of more than 48,000 alarms and 42,000 variables, display the status of the systems at different levels, detect any anomaly in the network and predict the volume of energy that will be generated according to future meteorology.
Below you can watch Rodrigo Corral, ALM Team Lead and Software Architect at Plain Concepts, explaining what it is, what it is for, and what are the benefits of using Digital Twins in the business environment.